
CEO NEWS & UPDATES
This page serves as a database for every monthly email that our CEO Andre sends to a handpicked group of people.
These emails serve as a recap for what has been done recently, what's cooking behind the scenes and what are generally. If you're interested in receiving the update, please enter your details below. We'll include you as soon as your entry has been reviewed.
OCtober 2024
As a software company, recurring usually means good things. All startups are after recurring revenue, after all. But we fight recurring. Because our users hate recurring tasks.
One thing frequently recurring task was customer data entry. We didn’t want to become the repository of customer data as nearly all our customers use CRMs, but some don’t and adding name, number, address etc over and over again became a drag. Now, simply find an order containing information from a common customer and add that to your list of Templates. The next time they give you a call or shoot you an email asking for new parts, start your process with that Order Template pre-filling your key tracking and Customer information into the system and fast track that order to production.
Oddly, users we asked preferred the template process to creating a database, which I did not expect. Another reminder to check your biases and talk with users frequently, if you needed it.

Another repeat process comes from having to click in and out of specific information sources to see detail. We started to address that a while ago with the roll overs for Runs in Flows, and we’ve started to expand that there and in Threads now. There are Tooltips for Events both in the Thread and in the “gantt” chart, as well as for Assets in Flows.
We have another improvement coming to Threads in a couple of weeks that saves literally 100+ hours per task. But I can’t talk about that quite yet. Keep your ears to the ground, and let’s meet up at Formnext and let me tell you all about it. Let me know when you’re free or pick a time that works for you.
If you’ve got some spare time before then, here’s a draft white paper I’ve written on the importance and means of capturing engineering Intent. Would love some feedback, if you’ve got any
September 2024
A post about how American Airlines treats their retiring captains got me thinking about how lucky we are to have a stable team and great alumni. You may get this email from me, but there are dozens of people that make the things in here happen.
That team reached another maturity milestone this month: Flows can now process runs with up to 1000 parts. That our customers need this feature tells you something.
That the platform is robust enough to handle it tells you another. I couldn’t be prouder and more grateful to the team.Of course, these changes also change the way the tool would be used. A thousand parts are very different from a few dozen. So, we changed the tool operates at the run level.
Next to viewing the list of parts in the build, you can now also aggregate the view at a design (or as we call it, at the “line item”) level. What’s more, amendments such as Non-Conformance Reporting, can also be done at that aggregate level. See below Gif of our new multi-part run feature.
While the team is working with our partners to deliver amazing products, I’ve been off to develop completely new business lines. One of them is with the DOD, building on our first award as a Prime last year. This year, we were awarded another contract and Josh (pictured below) and I just attended the kickoff in Ohio. It was amazing to see what the other companies (including 3D Printing OEMs etc) bring to the table, and I’m excited to help the Air Force build more advanced sustainment practices. Josh at the AF RSO IDIQ kick-off
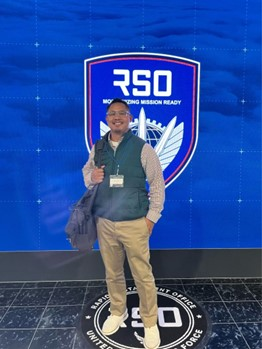

Authentise as a prime manufacturer is an interesting concept. Of course, we don’t actually manufacture anything ourselves – we subcontract that – but being involved in more detail obviously gives us a much better taste of what our other partners experience on a day-to-day basis. It tests our tools, and our understanding to the max.
And that helps us make it better over time.On that note, if you want to help us skip the “hard” learning – please reach out and give me and the team feedback in person. We want to hear from you. Any features you think should exist that don't?Hope to hear from you soon!
AUGUST 2024
Integration 🔁 - Authentise CEO Update
As the summer winds down (Happy Labor Day, America!) and my family close out the season at the cabin, it’s clear that while I’ve been indulging in some much-needed downtime, the wheels at Authentise have kept turning at full speed.
You might have caught the news—Authentise was among 67 companies awarded a U.S. Air Force Indefinite Delivery/Indefinite Quantity (IDIQ) contract with a ceiling of up to $1 billion. This is a significant milestone for us, and I know it raises some questions about our next steps. Let me shed some light on that.

About a year ago, we embarked on a significant journey with the Air Force by securing a production award. It was a first for us, and as far as we know, we’re the first software company in history to take on such a role. While we’re not the ones doing the designing or the physical production, we are responsible for ensuring that everything runs smoothly—managing subcontractors and delivering on our promise of better performance through data.
These experiences first led us to integrate Large Language Models into Threads and are now leading us to integrate Threads and Flows. That’s a major milestone for Authentise – our tools now cover the entire idea to part spectrum. That’s exactly what the DOD wants: Transparency and data
along the entire process.
With this feature you can jump into a detailed conversation about an order, tie in additional stakeholders and resolve key issues before you go to production. As part of this improvement, also expanded the comment feature to runs, and added the ability to assign users to specific tasks.
This is just one of a series of improvements we’re making to Flows driven by feedback from customers. Others include:
-
My Action Assignments for Downtimes and Line Items: Task assignments, which you’ve seen in the chat features, are now available for Downtime scheduling too.
-
Custom Fields Expansion to Runs and Downtimes: Tailor data capture to your needs by adding custom fields to your Runs and Downtime events, ensuring the right information gets to the right people.
-
Hyperlinks on Piece QR Traveler: A small but mighty update—quickly access orders or traceability reports directly from the traveler (when viewed digitally, of course).
These and a whole host of smaller updates prove that I can happily step away from the business for a while, and still succeed. I’m extremely proud of what the team’s done in the last month. It’s super exciting not only to see the vision come to fruition, but see the smaller, customer centric changes happen too.
Speaking of vision: Since I have to be in the US for DOD related work the week after IMTS, I’m skipping the event this year. I’m also meant to be cycling across the alps the weekend after, so I think it might be the right decisions – though all the prep notes on LinkedIn are giving me FOMO. I’ll be in Ohio and possibly DC in late Sept though, so let me know if you will be too. In the meantime, come to London or let’s meet on LinkedIn. I’ve been spending a bunch of time on the platform since my colleagues convinced me to give it more attention. It’s paid off – I’ve have a bunch of very interesting conversations there lately; even learning a lot about management.
See you there or IRL soon.
Andre
JUly 2024
Taking Ownership 🫡 - Authentise CEO Update
As promised, greetings from the Costa Rican coast, where I’ve been sunning myself with 100 family members. That may sound like a lot, but I heard from another additive industry participant that 1,000 members aren’t uncommon at their family gatherings. So we’ve still got room for growth.
The same is true for our user experience. Truth be told, we’ve intentionally invested in function over looks and experience. As a result, we’ve got the deepest functionality set of any workflow provider – who else can help you track all the way down to the environmental sensor data in your material storage location, for instance? But we know it can sometimes be a bit hard to find the things you need. And some of the interfaces look like they’re from the 90’s.
So we’ve been quietly looking at improving the look, feel and flow of Flows in particular. Recently you will have noticed our User Admin page received a big makeover and heavy users will know that many system “type” level resources can now be made on the fly, rather than having to build them all out before using them for your workflows to produce parts. We aim for each of these adjustments to continue to save your team clicks and minutes, each day that they’re using our app! (Cheeky watchers might have noticed our new Login page too)
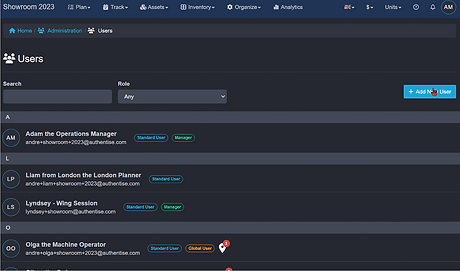

But that doesn’t stop us building net new capabilities too. For example, we’ve clarified ownership of Machine Maintenance Downtimes and Line Items. Owners receive curated lists of what they are responsible for on their own homepage. This allows for them to focus on exactly what they need to do, without getting pulled into all the other work in progress!
There are some other projects coming that I’m so excited to share with y’all. New features as well as new features. One of them that I can already tell you about is that the US Air Force has now awarded us an Indefinite Delivery, Indefinite Quantity agreement with a ceiling of just shy of $1bn. This is the next stage in our evolution to using our software to deliver a better part purchasing experience. I’m excited to share more with you as we’re awarded Task Orders under this agreement.
Maybe we can discuss in person? I’m currently considering to come back over the pond for IMTS. Will you be there?
Enjoy what remains of the summer.
Pura Vida,
Andre
JUNE 2024
Inventory Partners🚚 - Authentise CEO Update
I just got back from Rapid sicker than I was going there, so this email is both late and brief. It’s the post-Rapid energy buzz that’s got me writing this at all. While there’s a lot of talk about the doldrums the industry is currently in, there’s also excitement.
Part of that was due to partnerships, one of which was our announcement with UPM. Together, in an industry first, we’ve released a Vendor Managed Inventory extension to Flows AM! The tool allows consumable and services suppliers to additive manufacturers to collaborate much more closely.
They can provide detailed information of their delivery way before the materials or tools even arrive at a client site and can see the inventory movements inside of their facility so that they know when stock is low or build plates need to be picked up for resurfacing or disposal.

There are lots of reasons why this is an important addition to the additive industry. First, because it shows that the industry is maturing. The fact that the industry didn’t have these tools built into additive specific software is testament to the fact that we weren’t really thinking at scale.
Secondly, because of all the improvements these tools bring to AM manufacturers, including:
1. Increased Efficiency: saving you valuable paperwork time in cutting POs, calling up suppliers to find out where it is and more...
2. Improved Traceability: In the first example of this, build plate data (flatness, hardness, parallelism, surface roughness etc) was uploaded and made part of the build plate traceability record before the build plate was even delivered to the client site.
3. Financial Benefits: This tool enables consignment, which means the client only gets billed when the material is actually used. In addition, it enables suppliers to reduce the inventory they’re keeping at your site, which reduces their working capital and their ultimate cost to the user.
In short, it’s a win-win-win. So why not give it a spin – we’re offering this tool as a standalone or together with our material genealogy, which is also available in our workflow engine, Flows. I don’t usually pitch in this email but really – you should try this. It’s cool.
Now back to feeling miserable – this Man Flu is real and I have to shake it, as I’m meant to be writing my next mail all the way from Costa Rica.
Thanks,
Andre
MAY 2024
Carded 🃏 - Authentise CEO Update
Greetings from Georgia (country, not state), where I’m currently taking a break from cheese, cute old buildings, and museums to send you a postcard of a different kind.
It’s a fitting theme, because a tidy up of the Flows frontend has revealed quite a few cards across the platform in a shift away from the 2000’s style tables that used to dominate. The cards are now visible in main app for printers and post-processors, as well as the QR app.

he printer card displays both machine status information as well as material loaded, if any.
Card view now extends to post processors too
Cards exist in various forms in the QR app too, for example when handling materials

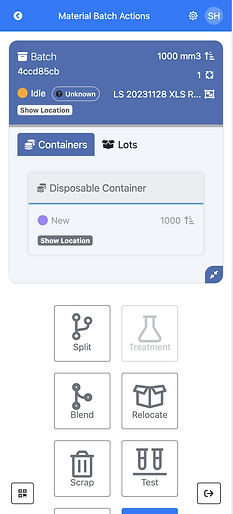
In short many places now have access to a view that provides a lot of contextual information at the drop of a hat. The list view naturally still stays available, but I have a suspicion that people will prefer the card view.
We also kicked off cards of a different type for Threads this month – templates. It’s natural that a tool that’s currently used to provide some structure to unstructured conversations would extend that structure into the foundation of all bureaucracy – reports such as Technical Data Packages, Model Based Designs, or structured reports of any other kind.
It’s exciting progress and I can’t wait to tell you more about it.
In the meantime, I’m hoping for some cards myself – from the tech team. They’re meeting near Birmingham next week, while I’m in Georgia. It’s amazing to see such a physical distributed team come together. I’m delighted, that so many US people could come (even though a number of them didn’t have passports 🤯
And of course, I’ll be pulling out my (credit)card this month as I’m heading to LA for Rapid. Putting the show into a vacation destination in the summer is one of the less enjoyable trends of the tradeshow wars we’re currently going through. I wish the industry would just get together. But if you’re there – let me know, it would be great to meet up. We’ve got a great announcement coming up 😉.
See you there.
Andre
APRIL 2024
Staying in Control ✨ – Authentise CEO Update
I keep on hearing about how terribly the industry is doing. We don’t see it. Quite the opposite: We keep on beating our record quarters by significant margins. We’re winning almost every deal we’re going after, and there’s no shortage of them..
I hear machine vendors are particularly affected (one older, privately held German maker just borrowed money for the first time) by the downturn. That may be due to their blatant overselling in the last decade. Not only did they SPAC at valuations 100+ times their revenue on outsized projections, but they also pushed machines into the immature market into immature market.
Apparently, there are now 800+ metal additive machines in the Los Angeles area alone. Most those machines will be operating extremely low OEE. Until that capacity starts to sweat, machine sales will continue to underperform.
Maybe machine OEM’s would have been better served, listening to the customer, incrementally improving their machines and really focusing on making them production ready rather than overselling? That’s what we’ve been doing for the last decade, and maybe that’s why things are different for us?
2 of the latest changes are an example:
-
Secure Build Checkout: Manage your build prep process on local, networked PCs with our Secure Build Checkout. Designed to control and automate a portion of the additive printing process that was previously controlled through manual intervention. Check out files and pull them directly from Authentise onto a Build Prep PC where you can load them directly into various Machines’ Build Prep Software (and therefore push the files to the machines). Changes made to the files while checked out are then reuploaded to the Authentise platform for traceability and record keeping.

-
STEP File Support: Previously only available via our paid File Conversion Module, support of Step files is now available to all users. If you’re not seeing it in your bureau, contact us at support@authentise.com we will get you taken care of!
See: simple, reactive, successful. We listen to our audience, rather than being beholden to our shareholders. Maybe that’s because our employees are our main shareholders? Not that it helped the German company 😉
Here’s to more sustainable growth, together!
Andre
March 2024
Different Views 👓
Russia’s aggression in Ukraine and the monumental suffering there have made me think about how differently people can perceive a situation. In the case of Ukraine, the aggressors view is obviously deeply flawed. However, it’s not always so clean cut. There are often many different legitimate ways of looking at the same data set, for instance.
We’ve held this view for a long time – as displayed with integration with Power Automate. It gives every Authentise user the opportunity to output data in the way they want to see it: personalized dashboard, report or alerts for managers, shopfloor associates, sales and others.
We’re now taking this dual view approach beyond simple reporting: This month, we’re releasing our Order based GANTT. Previously the GANTT in Authentise only reflected Machines on the Y axis. That of course benefits shopfloor associates who need to plan runs, but it makes it difficult to see what the progress of orders or parts are.
Enter the Order/Part based GANTT. In this view, Orders appear on the Y axis, and can be expanded to reveal the constituent parts. The X axis is naturally still time, but you can now see order completion in Order rows, and the individual part step completion elsewhere.

The order based progress bar is helpful elsewhere: It will be included in the Order too, to give a faster insight into current status. We may do the same with the part-based view too.

I’m glad I get this once-a-month chance to explain our thinking and resulting actions. But I’m often surprised how much telling there is to do. This month we’ve done a couple of online webinars and sessions that go a long way into explaining what we are doing: One with McCad Café, which talks about the origins and product at a high level, and another with SME in preparation for their Smart Manufacturing Experience event in Detroit in June. That one was particularly exciting as it included Nick Weeks from Carpenter Additive, producer of metal powders and customers of our newly acquired Elements software suite. We had a really great discussion about the reasons for, and the struggles with, deployment of digital tools. If you have a moment, listen in and let us know what you think: What parts of our story are still unclear?
If you’d rather meet IRL (In Real Life, for those without younger siblings or children to keep you hip), there’s a couple opportunities for that too. For the first time ever, we’ll be at 2 events, on 2 continents, at the same time.
The first, naturally, is AMUG in Chicago starting this Sunday. I’ll be there, along with Derek and Celina. If you want to meet there, come to Booth 34, Salon D, or find a time to meet me here.
The second is MACH in Birmingham. We’ll be there for one day only (April 5th) to start talking with innovation friendly manufacturers about how our data driven tools can help make non-additive operations more agile too. Meet us at 6-820n or reach out to our team: Nick, our head of strategic projects, will be there, along with (🥁drumroll please) Keith.
The announcement that Keith has joined us from Hexagon (along with an illustrious list of former companies including Autodesk, Siemens, Oracle and more) is hot off the press and possibly the most exciting news of the year. We’ve been looking for somebody to really take ownership of the non-additive portfolio. We truly believe that the lack of legacy, increased data and lot size 1 that’s shaped additive has something to bring to a supply chain strained by the need to be flexible. Keith’s proven ability to listen carefully and distill the requirements into products, along with his staggering experience, will turn that belief into results.
Keith is by far not the only person who’s joined Authentise. Along with him, Andreea (marketing) and Ash, Marshall, Ayoub, Ameya, Tyler and Grigorii (all development) are joining Authentise within an 8-week window in a sign that we, hopefully, have broken through a glass ceiling in hiring and should be able to accelerate feature releases even further.
So, as always, there is much excitement and much to do – yet another example of 2 views of the same coin.
Hope to see or hear from you soon.
All the best
Andre
February 2024
ua Friendship 🤝
I wrote the first version of this update without mentioning Ukraine but it doesn’t sit right. At this time, it’s the primary thing on our minds. To see a ground war perpetrated by a criminal psychopath turning the lives our friends, coworkers and fellow Europeans upside down and, in some cases, costing it, is almost too much to bear. We’ve been watching in stunned silence but that hasn’t stopped us from doing something. We’ve checked in with our colleagues regularly, supported the humanitarian effort (here’s a good list if you’re interested), in some cases offered personal support for housing and visas, and are in the process of formulating policies that will stop Authentise from doing business with any organization related in any way to the Russian state.
While friendship with Ukraine is what drove the theme of this month, it’s actually a good theme for what happened: Of course, we announced our acquisition of Elements, which I expect you’ll have seen. That deal alone of is transformative for Authentise: It’s our first step outside of the additive world, we’ve gained some really interesting new clients and of course, some wonderfully talented team members. It’s a really exciting time for Authentise.
The fact that we’ve been able to bring other companies on board speaks to a maturity of the company that I didn’t think was possible before. We had another proof of that this month, with a few major final deliveries accepted. Of course, that doesn’t mean we’re finished with our deliveries. We constantly evolve with our partners, as you can see with this month’s updates:
Financial User
We’ve added another group type that is now permitted to see financial data such as price or margins. All other users won’t be able to see those anymore.
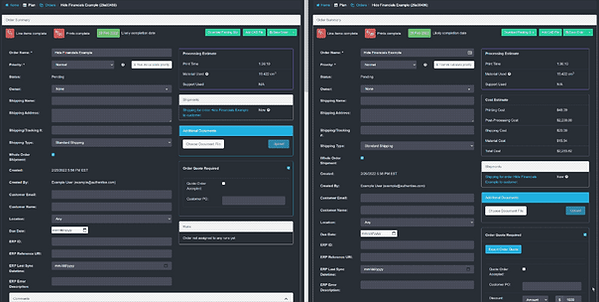
When an action is assigned operators get an email and the tasks appear on the dashboard when they log in to the system. Completing a task is just as easy. Operators simply log in and click on the task in either the dashboard or the full task list, to be taken to the specific section and task.

In the vain of simple but effective updates, the final change I want to highlight is that duplicating workflows now also duplicate work instructions. I hate to sound like a broken record but these kinds of updates are what turns us from a great system to a truly effective one. We’re so grateful that we can continue to learn from our clients in this way.
There’s more to report. We’ve got a very key hire we’re excited to learn. But more on that next time. If you have any news in the meantime, I’d love to hear from you.
Speak soon,
Andre
January 2024
Learning Together 🤔
I started this year with a warm January (my wife “persuaded” me to move to Portugal Q1 to catch a break from grey UK weather) by reflecting on our hits, misses, and learnings from last year. So, it’s no surprise that we started the year (while wrapping a few big deployments) by releasing quick win features that we’d skipped in 2021. These are a direct reaction to customers' feedback and the kind of features that I like to see most. They include:
Interactive Queues Page: This allows users to jump from the GANTT chart right to QR traveler and the app, making the printing out of travellers unnecessary if required.

Unplanned Downtimes: Often times these events occur when you're not looking or planning. Unplanned Downtimes are now easily recordable.

"Select All" when doing Production Changes: This accepts the reality that parts are often processed as a group.

We’ve also enabled users to override Run Time Actuals since realities on the shop floor mean that data must be easily correctable and overridable at the source.
Listening closely to customers is our superpower. It’s what made us the largest (by revenue) independent additive workflow provider and what will sustain our growth. So, while these updates seem small, they are an excellent representation of what we are best at, and what is most meaningful to our customers. Go team!
Great start to the year!!
Andre