Extending the Digital Thread to Materials reduces waste and total cost while increasing reliability and transparency.
Philadelphia, PA, 23 September 2020 – Authentise (www.authentise.com), the leader in data-driven workflow tools for additive manufacturing, has released a major feature update to simplify the digital tracking of material powders for additive manufacturing.

Material Management enables customers such as Boeing to track all actions associated with the material, such as sieving, blending, testing, or printing, to enable a full digital thread of the material. Operators can update the status seamlessly using apps on handheld devices while full reports and details, such as a full material genealogy tree, can be viewed in the browser. A tight integration with the Authentise Manufacturing Execution System (AMES) associates the material traceability report with any part printed on the machine it was loaded into. This enables detailed end-to-end digital thread that accounts not only for the full material history but also operator actions, machine data, and more.
“Digital Material Management is the missing piece of the puzzle for us,” says Miguel Zavala, Project Leader in Laser Additive Manufacturing at TWI Ltd in the UK. “As a certified Lloyds Register lab, we have to prove that we’re following the right process at all times. The combination of AMES with a seamless material tracking tool delivers full digital traceability of not only what we’ve done but everything that has happened to the part. We can use that data to improve our processes, provide automated reports to clients, and work with our partners to develop better machines, materials, processes, and designs.”
“We’re excited to be the only independent provider with an end-to-end digital material and part traceability solution,” says Andre Wegner, CEO of Authentise.
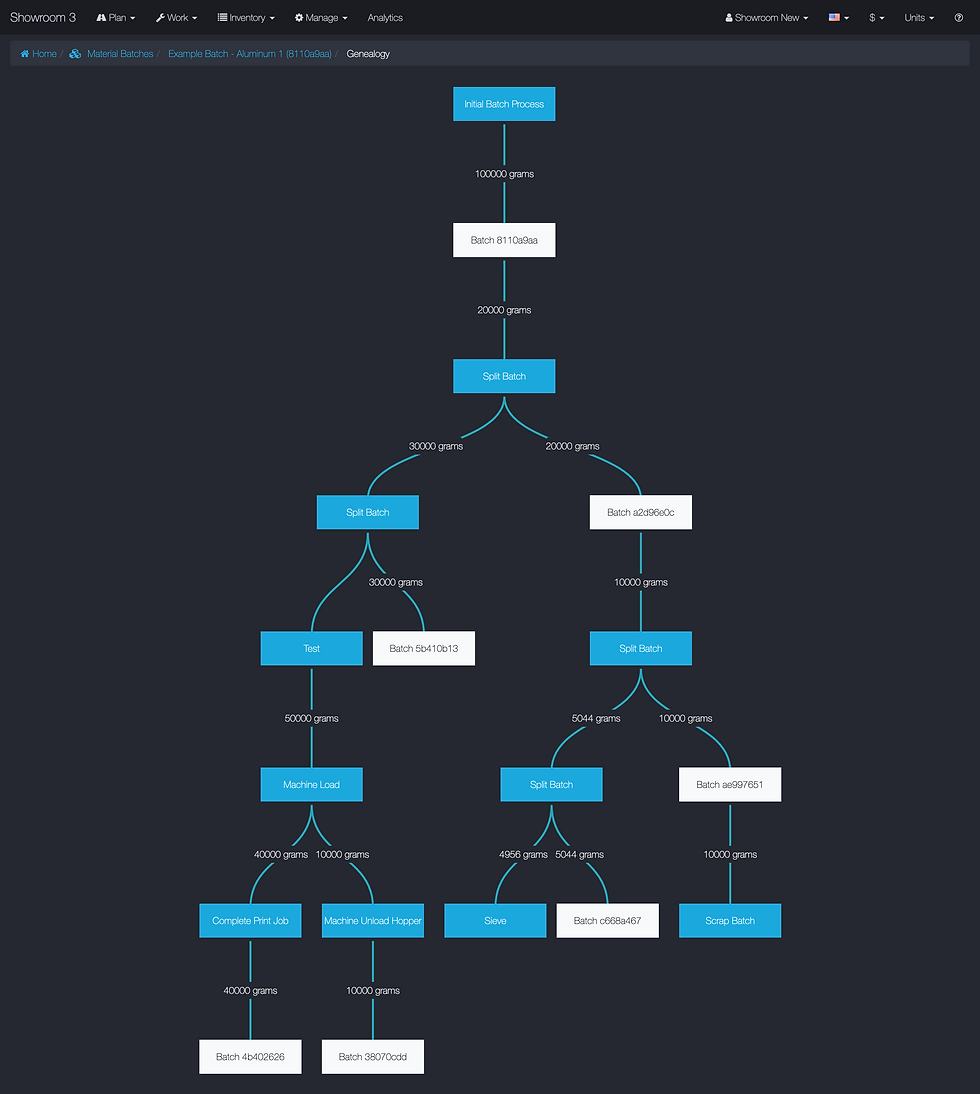
“There’s still so much we don’t know about the additive process: How do storage conditions affect end part quality? How many times can we recycle, under what conditions?
As a result, too much money is wasted as we default to the most secure and expensive options. Too many parts still end up being printed with virgin powder unnecessarily. The integration of our unique ability to draw together data from machines, operators, testing, and now materials finally gives us the tools to understand these processes fully, and explain them to our partners.”
For information, please contact: Andre Wegner, CEO Authentise, andre@authentise.com, +1-650-861-7077
About Authentise
Authentise delivers data-driven process automation software for additive manufacturing. Its two products include AMES, a workflow management engine using machine data for automation, and 3Diax, a platform of manufacturing-related software modules. These tools help Boeing, Ricoh, 3M, Danfoss, and others at the forefront of R&D, prototyping, and production to reduce effort and cost, improve traceability and transparency, and deliver quality. The products also serve as their core contextual data engine in manufacturing, enabling them to easily build connected Industry 4.0 solutions. The company was founded in 2012 in San Francisco and operates offices in Philadelphia, London, and Kyiv.
About TWI
TWI is a world-leading research and technology organization. Bases in the UK, North America, South East Asia, China, Australia, Central Asia, India, and the Middle East see 800 staff provide technical support in joining and technologies such as material science, structural integrity, NDT, surfacing, electronic packaging, and cutting. Services include generic research, contract R&D, technical information, consultancy, standards drafting, training, and qualification. TWI offers a single, impartial source of service for joining engineering materials. TWI is internationally renowned for its multidisciplinary teams that implement established or advanced joining technology solving problems at any stage – from initial design, materials selection, production, and quality assurance, through service performance and repair.
コメント